Case study: German Organic Farm Store Aims to Switch-Over Completely to Natural Refrigerants by 2021
Thanks to positive experiences with Isobutane (R600a) and CO2 (R744), Eekenhof in Varel is planning to change remaining cooling equipment to natural refrigerants by next year.
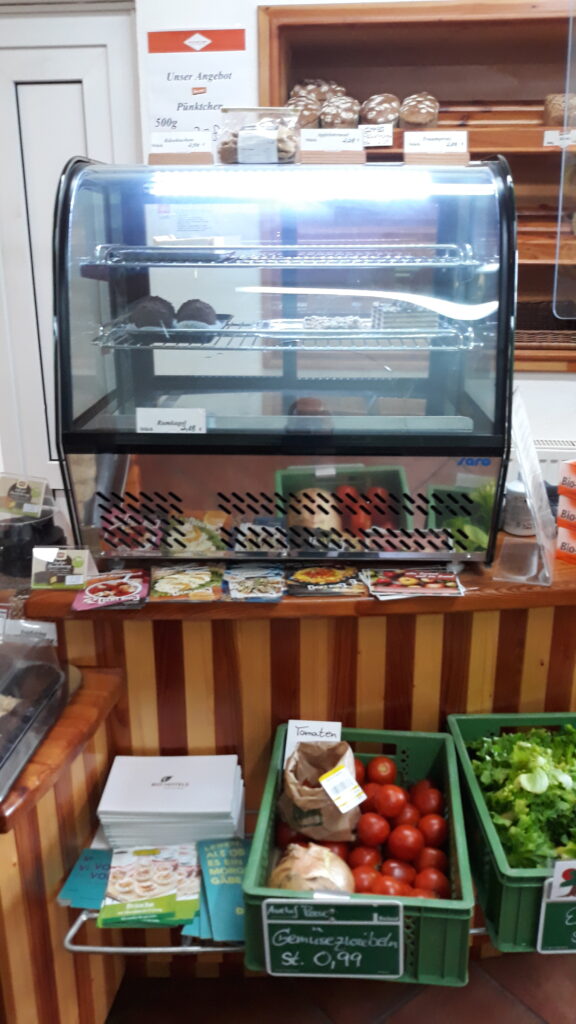
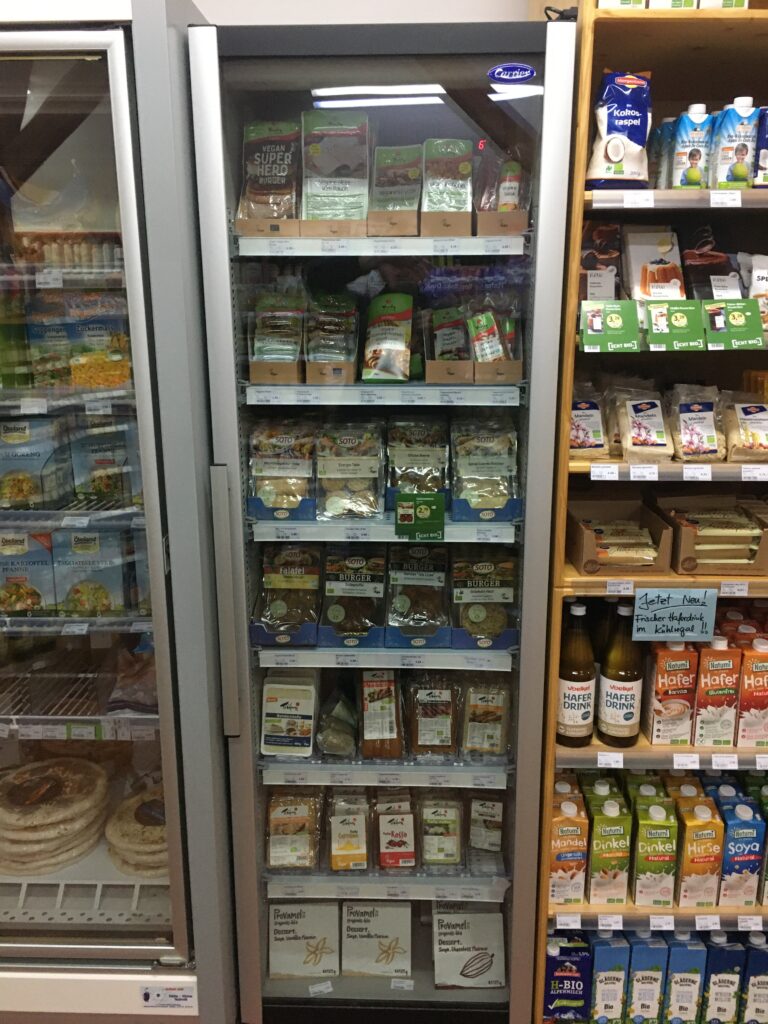
About the store
The “Eekenhof” farm in Varel, Germany was originally build in 1750 and the family who runs it now, has owned it since 1860. Klaus Leiter is the current owner. He took over the farm in 1988 and started farming organically the next year in 1989.
A single grocery shop for organic products was added in 1994. The shop has 14 employees (with worktimes between 7,5 and 34 hours per week) and supplies a full range of fresh and dry products – around 2,500 in total. About 20% of the sales volume is gained with products from within the region. It also offers delivery services of fresh fruit and/or vegetable boxes for individuals, primary schools, and companies.
Expanded cooling needs
The first shop in 1994 occupied only 70m2 of space and was equipped with two cold storage units and a cheese bar, all supplied by one cooling system and a few stand-alone fridges.
In 2014, the shop was expanded to 120m2 area, adding an additional multi-deck merchandiser with doors to the cooling system. In 2016, a second cooling system was also added, supplying the deep freeze multi- deck, as well as an ice cream freezer, a single swing-door cooler, a cake-cooling counter, and a stand-alone freezer for storage at the back – the last three are running on natural refrigerant R600a.
In 2017, a cooling cabinet with three rooms (total size 62.5m2) was added in
a different building to store the fresh vegetables produced on the farm. Each room is adjustable in terms of temperature, depending on the product stored. The new system runs on CO2 (R744) and works well with no problems so far, according to Leiter.
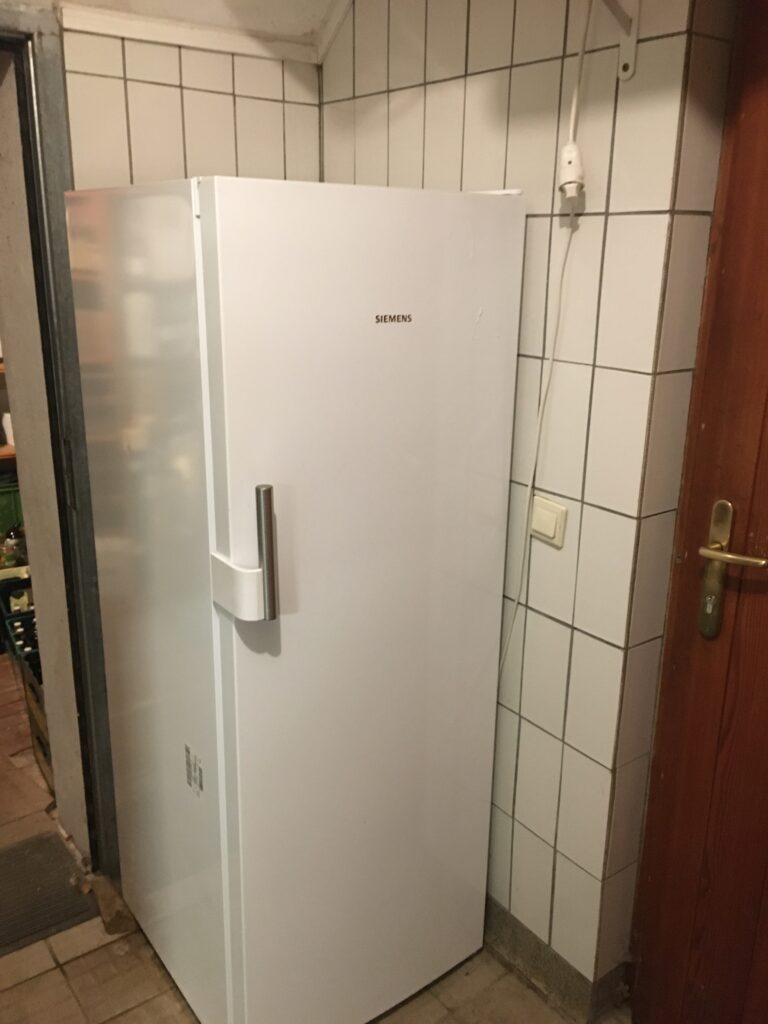
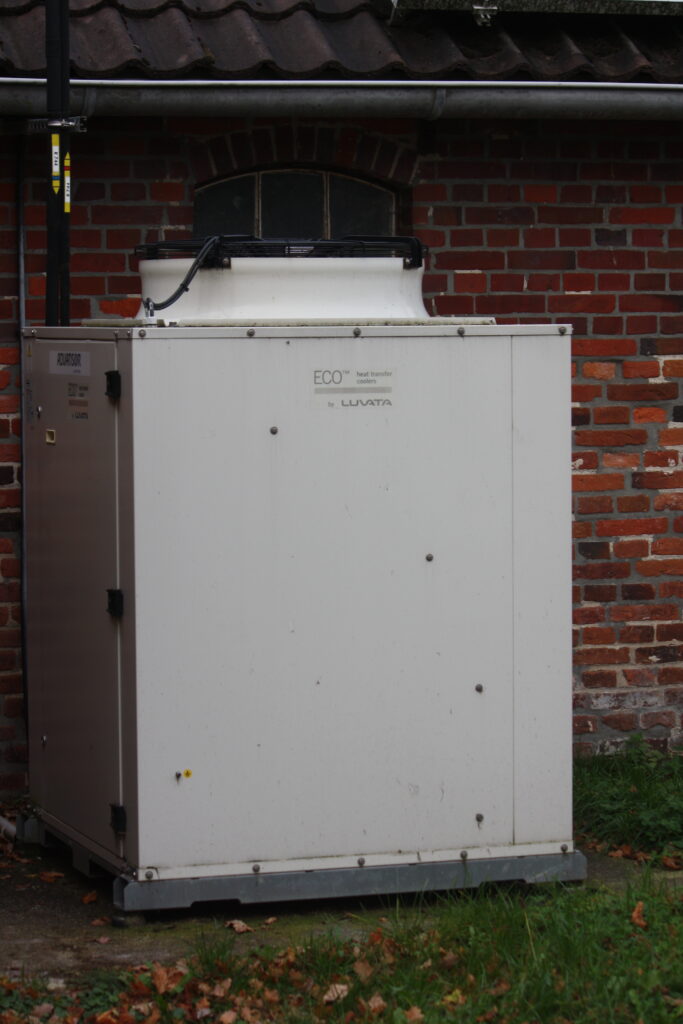
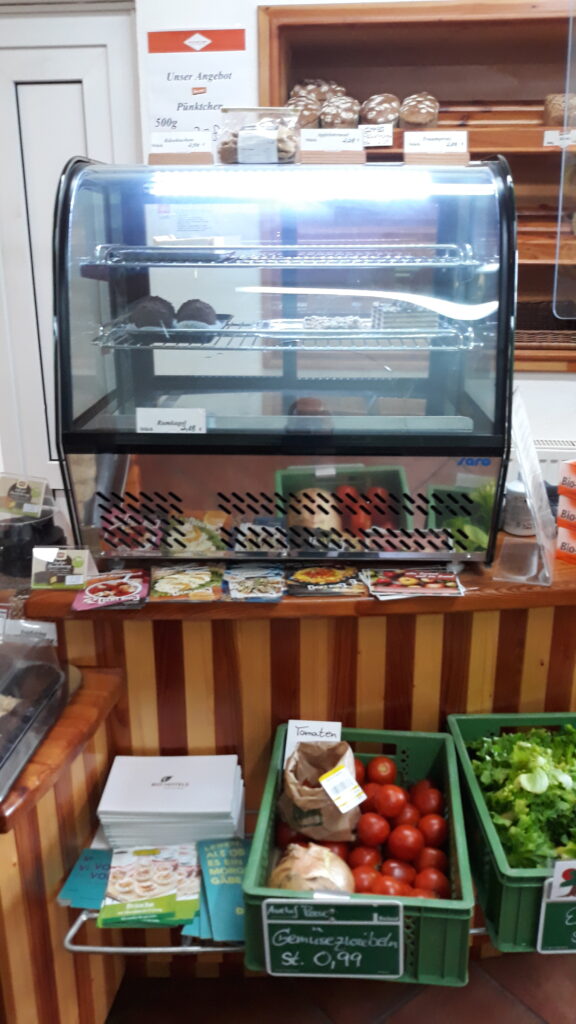
Sustainability matters
The farm also has a photovoltaic (PV) solar system, built in 2010, which produces around 29,000kWh/year – about 15,000kWh is used directly. Around 50% of Eekenhof’s total annual energy consumption is used for cooling needs.
“Since the Eekenhof considers sustainability as a very high priority, switching to natural refrigerants became an area of focus some years ago already,” explained Leiter. The high global warming potential (GWP) of the HFC refrigerants their existing systems are using, as well as the rising prices of e.g. R134a, were key motivating factors for upgrading the cooling systems.
The positive experiences with R600a (since 2013) and CO2 (since 2017) convinced Eekenhof to switch all cooling equipment from fluorinated gases to natural refrigerants (preferably R744) in one step in 2020. Unfortunately, the Covid-19 pandemic has delayed the process to 2021.
The plan is to install a new natural-refrigerant based system that handles both the cooling and freezing needs, An integrated heat recovery system will be included to supply the heating needs of the people living on the farm.